Seven technology breakthroughs
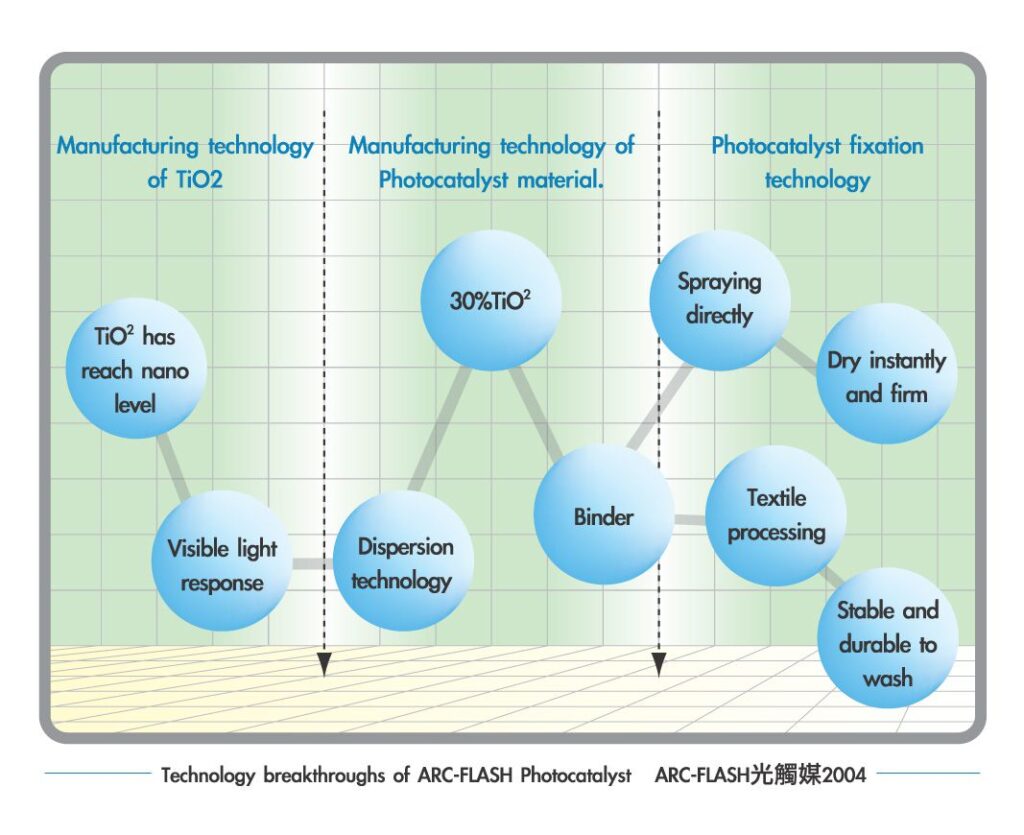
Earlier in 1992, the R&D team of ARC-FLASH had realized that technology breakthrough is a must for producing competitive Photocatalyst with high quality. For more than ten years since then, those excellent developers of ARC-FLASH have meet many “mission impossible” challenges. After continuous efforts, there have been notable technology achievements in both Photocatalyst material manufacturing and fixation of textile processing and spraying. These technology breakthroughs are the secret reasons why the market share of ARC-FLASH reached over 90%.
It must overcome obstacles such as the technologies of manufacturing TiO2 /Photocatalyst materials and Photocatalyst fixation in order to produce Photocatalyst with a high quality. After improvements for many times since 1995, ARC-FLASH Photocatalyst in the current market is the fourth generation product, which has many advantages such as small-diameter TiO2 with high concentration, visible light response, being able to spray directly onto the surfaces of any objects and getting dry and firm immediately. All these are the attributions of ARC-FLASH developers’ relentless efforts in thirteen years since 1990.
To ensure enough specific surface area (the proportion of volume to surface area) to be effective in micro- world, the diameter of TiO2 must be controlled under nanometer. According to the reports by Scientific American in 2002, the general crystallization of TiO2 is between 20~250nm, which is not effective. In fact, TiO2 will work only if its diameter is under 7nm. It is because in 3-D space, the smaller the particles’ diameters are, the closer they will line, and the increase of specific surface area will cause more sensitive reaction. The average diameter of TiO2 in ARC-FLASH Photocatalyst is under 7nm, which could result in a rather big specific surface area, and a high effectiveness per unit.
In 2000, ARC-FLASH was the first to overcome the limit of only UV light being able to activate Photocatalyst and successfully developed “visible light responsive” feature working with both the ultraviolet of 300~400nm wavelength and the visible light of 400~800nm. Thus ARC-FLASH started a new era of “visible light responsive” Photocatalyst. In the past, Photocatalyst could only be triggered by ultraviolet light, which confined the application of Photocatalyst. It became necessary to install ultraviolet lighting tube if there was no such light in order to inspire Photocatalyst for reaction. But now, even in an environment lack of natural light or at night, it can also use visible light (fluorescent lamp or bulb) for reaction since the fourth generation Photocatalyst increases the applying range and cut the cost of adding illuminating devices.
The quality of Photocatalyst (i.e. product efficiency) is mostly determined by the TiO2 level in materials; which means, the more TiO2 it contains, the better quality and efficiency it will have. The TiO2 concentration in ARC-FLASH Photocatalyst materials reaches 30% and it obviously has an edge over other Photocatalysts with a TiO2 level less than 1%. TiO2 is white and of solid state, so TiO2 concentration in material can be judged from its appearance. When the TiO2 level is low, the material is transparent and watery; however, it will become white once TiO2 is over 10%. The more TiO2 it contains, the thicker the material will be. The TiO2 concentration of ARC-FLASH Photocatalyst reaches 10%, thus it looks like thick milk.
It is very hard to improve TiO2 level of Photocatalyst materials technically, that is why TiO2 concentration of Photocatalyst in current market is
universally less than 1%. Because the density of TiO2 is higher than water, it will easily precipitate and condense in water in a large amount. So as to improve TiO2 level successfully and avoid precipitation, it must depend on a good dispersion technology. Although precipitation is inevitable, with a good dispersion technology it could be dispersed evenly after shaking. ARCFLASH Photocatalyst inside a container will become gelatinous after placed for several days but it will be dispersed easily by shaking. ARC-FLASH Photocatalyst owns a good dispersion technology so that it can raise TiO2 level without affecting the following application.
Binders are supposedly used to fix Photocatalyst on the surface of objects but few Photocatalysts applying in the market are using them. Because binders are organic compounds and would be decomposed by Photocatalyst, most manufactures have to give up binders without being able to overcome the obstructions of their applications, which means they cannot fix Photocatalyst by spraying directly. Thanks to the leading technologies, ARC-FLASH Photocatalyst can combine with binders without decomposing them. Through special fixation technologies, it becomes very easy to fix ARC-FLASH on surfaces of any objects by spraying directly.
ARC-FLASH is one of the few professional Photocatalyst manufacturers with the fixation technologies of direct spraying globally and due to this ARCFLASH can provide a complete spraying service. The special spraying gun of ARC-FLASH is particularly made by Meiji Industry of Japan and can spray 1μm bubbles covered by the binder layers, through which TiO2 will attach on the bubble surfaces. Once bubbles are sprayed and attached on the surface of objects, it would be extruded and become half-sphere. Then the surface tension caused by the pressure inside bubbles will push TiO2 forward and stay on the bubble surfaces to meet light for reaction.
Owing to the fixation technologies, ARC-FLASH Photocatalyst can be directly sprayed on the surfaces of any materials including organic matters. The decomposition problem is wisely avoided because ARC-FLASH Photocatalyst will not directly contact materials, unlike other Photocatalysts. It is unnecessary to take steps of protecting organic materials by coating inorganic matters before processing. The technique simplification and extension of application ranges are the fruits brought by the fixation technologies of ARC-FLASH Photocatalyst.
Photocatalysts of other brands are watery and hard to dry after spraying and even need being heated under high temperature, which are quite inconvenient.Unlike them, ARC-FLASH Photocatalyst can dry in seconds after spraying on rough surfaces (e.g. wall, wood), and in less than 30 seconds on glossier surfaces (e.g. tiles, marble), so the feature of drying instantly o makes it very
convenient to apply without affecting the construction environment.
ARC-FLASH Photocatalyst will not be erased by touch after being dried, and its hardness could reach the maximum (Pass the standard of CNS, scrubresistance 2000 times) in 10~14 days, which is even harder than the paint of automobiles. The layer will last long on the surfaces of objects and will not be damaged unless being rubbed with hard things.